MORC MSP-32 Linear Rotary Type Intelligent Type Valve Smart Positioner
Characteristics
■ Use piezoelectric valve electric pneumatic conversion structure.
■ Suitable for hazardous area by intrinsically safe electronics.
■ Easy to install and auto-calibration.
■ LCD display and on board button operation.
■ Fail safe function under loss of power, loss of air supply and loss of control signal.
Technical Parameters
ITEM / MODEL |
MSP-32L |
MSP-32R |
|
Input Signal |
4 to 20mA |
||
Supply Pressure |
0.14 to 0.7MPa |
||
Stroke |
10~150mm(standard);5~130mm(adaptor) |
0°to 90 |
|
Impedance |
450Ω(without HART),500Ω(with HART) |
||
Air Connection |
PT(NPT)1/4 |
||
Gauge Connection |
PT(NPT)1/8 |
||
Conduit |
NPT1/2 ,M20*1.5 |
||
Repeatability |
±0.5% F.S. |
||
Ambient temp. |
Normal: |
-20 to 80℃ |
|
Normal: |
-40 to80℃ |
||
Linearity |
±0.5% F.S. |
||
Hysteresis |
±0.5% F.S. |
||
Sensitivity |
±0.5% F.S. |
||
Air Consumption |
Stable condition:<0.0006Nm3/h |
||
Flow Capacity |
Fully open:130L/min(@6.0bar) |
||
Output Characteristics |
Linear (default); Quick open; |
||
Material |
Aluminum Die-casting |
||
Enclosure |
IP66 |
||
Explosion Proof |
Ex db IIC T6 Gb ; Ex tb IIIC T85℃ Db |
Electro-pneumatic control principle:
The P13 piezoelectric valve electrical control module imported from Germany HOERBIGER is selected. Compared with the traditional nozzle-baffle principle positioner, it has the advantages of low air consumption, low power consumption, fast response and long life.
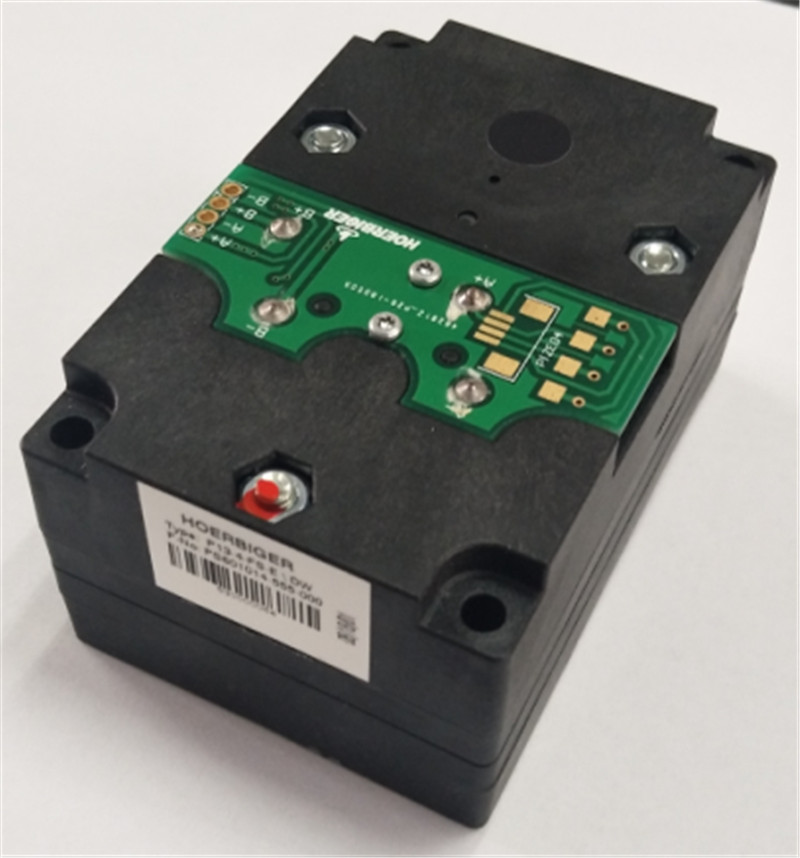
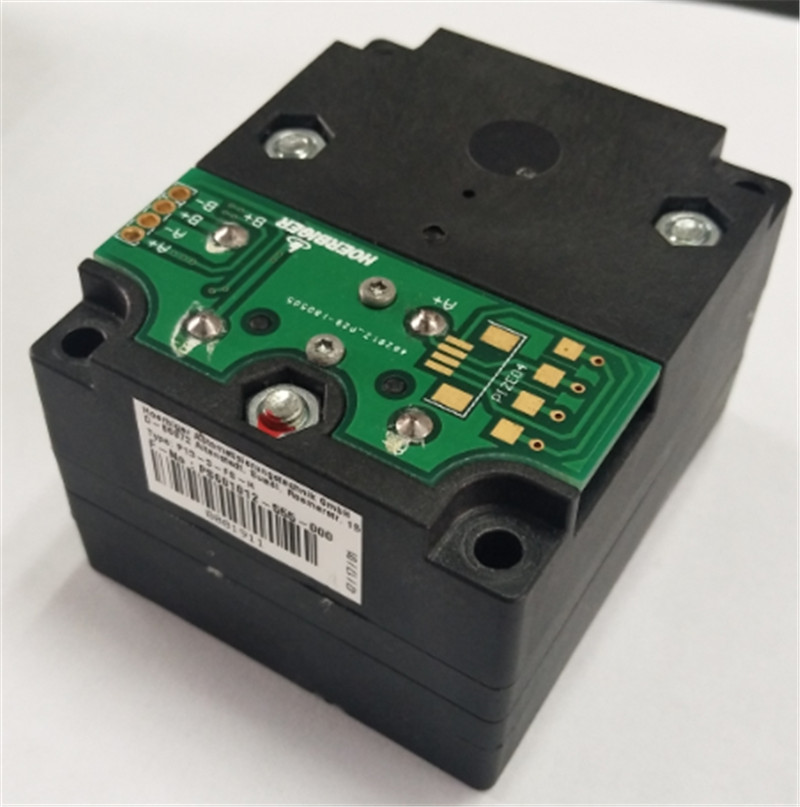
Main Features and Functions
•LCD display enables users to monitor the positioner status.
•Positioner operates normally during sudden changes in supply pressure and / or high vibration environment.
•Low air consumption level and low voltage use (8.5 V) yield to lower plant operating costs. The MSP-32 is compatible with most of controllers.
•Variable orifice can be used to minimize the hunting occurrence and optimize operating conditions.
•Valve system feedback is greatly improved by the accuracy and fast response of the MS-P-32
•Different valve characteristics can be adjusted - Linear, Quick Open, Equal Percentage, and Custom which user can make 16 points characterizations.
•Tight Shut - Close and Shut - Open can be set.
•PID parameters can be adjusted in the field without any additional communicator.
•A/M switch can be used to direct supply air to the actuator or to manually operate the positioner or valve.
•Split range 4-12mA or 12-20mA can be set.
•Operating temperature is -40 ~ 85°C.
Safety
When installing a positioner, please ensure to read and follow safety instructions.
Any input or supply pressures to valve, actuator, and / or to other related devices must be turned off.
Use bypass valve or other supportive equipment to avoid entire system "shut down".
Ensure there is no remaining pressure in the actuator.
MSP-32L Installation
MSP-32L should be installed on linear motion valves such as globe or gate type which uses spring return type diaphragm or piston actuators. Before proceeding with the installation, ensure following components are available.
•Positioner unit
•Feedback lever and lever spring
•Flange nut (bottom side of MSP-32L)
•4 pcs x hexagonal headed bolts (M8 × 1.25P)
•4 pcs x M8 plate washer
Why choose us?
Using the cutting-edge piezoelectric valve principle, the smart positioner has a series of advantages and is the first choice for controlling valve opening in pneumatic systems.
One of the main advantages of the piezoelectric valve principle is the low power consumption, i.e. low air consumption. This in turn reduces the operating costs of the locator. In steady state conditions, the inlet and outlet ports are closed, so the consumption of the air source is minimal compared to the nozzle principle.
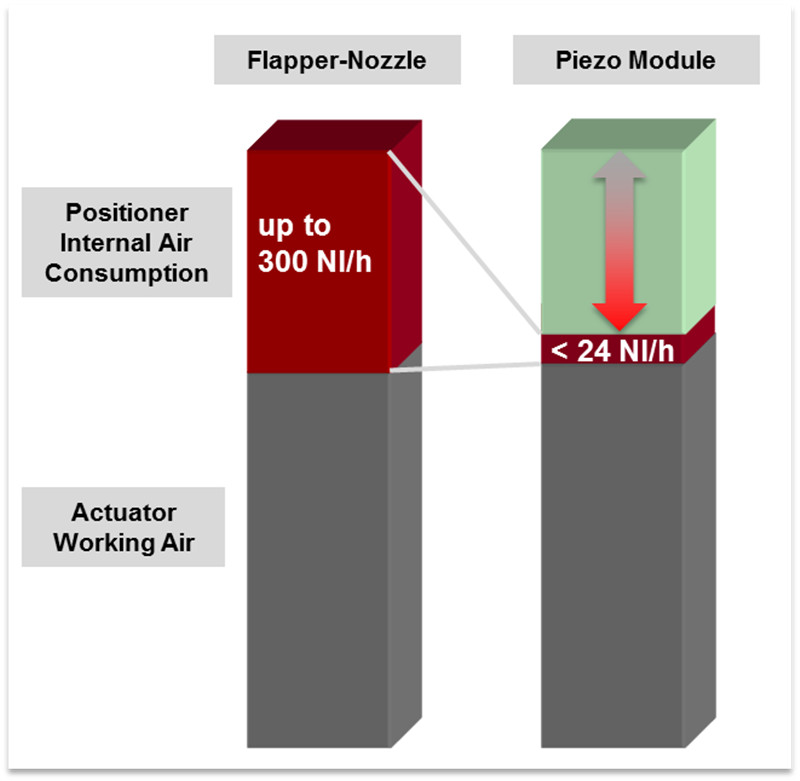
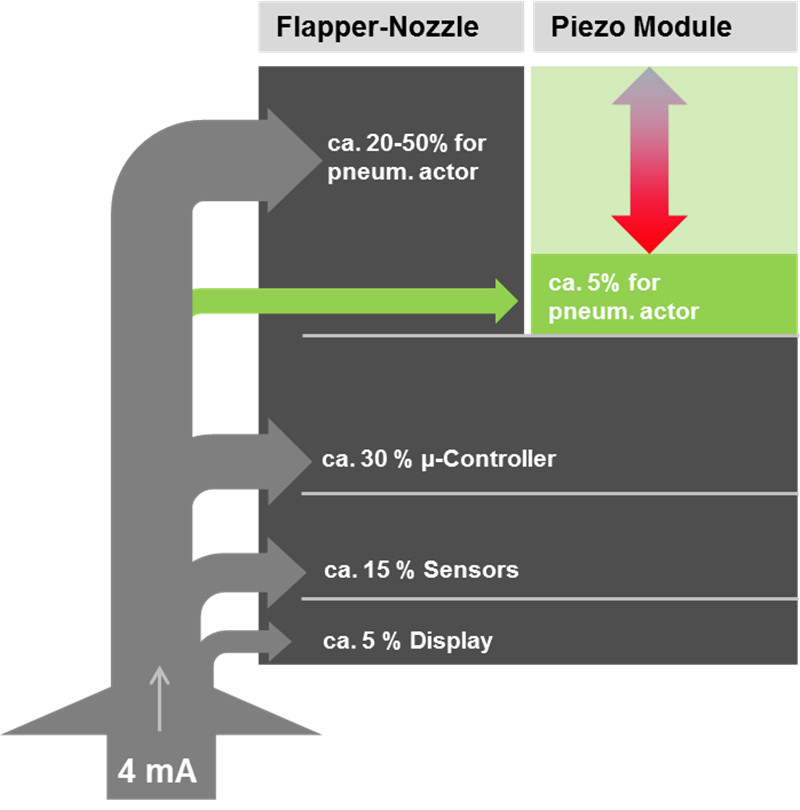
Another feature that distinguishes the piezoelectric valve principle is its high vibration resistance. The overall module structure of the positioner has few moving parts, no mechanical force balance mechanism, and good anti-seismic performance. This feature is especially important in applications where vibration can cause disturbances in the system.
Fast response times and long service life are other benefits of the piezoelectric valve principle. Response times as low as 2 milliseconds make the positioner highly responsive to changes in system parameters. In addition, the operation life of the piezoelectric module is at least 500 million times, ensuring reliable and long-lasting performance.
With its advanced features and advantages, the intelligent positioner is the main device for controlling the opening of the valve in the pneumatic system. It can accurately adjust any opening of the valve, and is an essential tool for adjusting the flow of air or gas. This smart positioner offers unrivaled performance, reliability and economy, making it the first choice for a wide variety of industrial applications.
In conclusion, combined with the product features and description, the smart positioner using the piezoelectric valve principle is the best choice to meet your valve control needs. Low operating costs, strong vibration resistance, fast response time and long service life are all key features that set this product apart. If you're looking for a smart locator with unrivaled performance, you've just found it. Choose our smart positioners based on the piezoelectric valve principle today and experience effortless valve control.